
Le processus
Notre processus industriel est l'étape centrale au coeur d'une boucle d'économie circulaire, écologiquement vertueuse, dans laquelle les emballages sont recyclés localement à plus de 80%
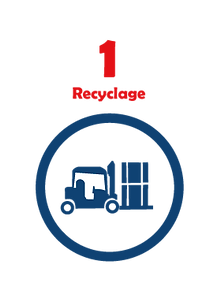
PHASE D'APPROVISIONNEMENT EN MATIERE PREMIERE
GEMDOUBS recycle des papiers et des cartons récupérés, provenant à :
- 30% des emballages ménagers récupérés par les collectivités (Grande Région principalement) ;
- 70% des emballages produits collectés auprès de la grande distribution (agroalimentaire...) et de l'industrie. La matière première est livrée sous forme de balles compressées, chacune pesant entre 300 et 1500 Kg environ, qui sont stockées dans le parc à balles.
![]() |
---|
![]() |
![]() |
![]() |
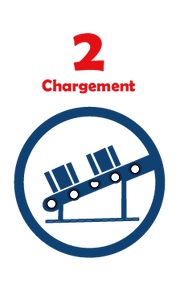
PHASE DE CHARGEMENT
Les balles sont acheminées par des caristes vers le tapis élévateur, qui les monte dans la cuve du pulpeur, où elles sont défibrées.
![]() |
---|
![]() |

PHASE DE TRITURATION
Lors de la première étape du processus de trituration, les balles sont broyées avec de l'eau par le rotor du pulpeur. Le papier est ainsi défibré, la fibre de papier (cellulose) est séparée d'une majeure partie des déchets - plastiques, métaux, boues...
![]() |
---|
![]() |
![]() |
![]() |
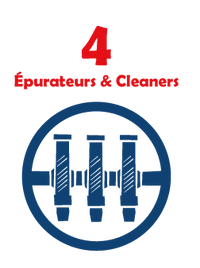
PHASE D'ÉPURATION
Les épurateurs poursuivent ce travail de manière plus approfondie en ciblant différents types d'impuretés.
Les cleaners terminent la phase de traitement en séparant définitivement les plastiques, les agrafes, les colles, pour ne conserver que les fibres de cellulose servant à la fabrication du papier. On obtient ainsi de la pâte à papier.
![]() |
---|
![]() |
![]() |
![]() |
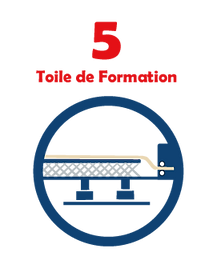
PHASE DE FORMATION
Le processus de fabrication du papier commence. La pâte à papier, composée d'eau et de fibres, est projetée sur la toile de formation, sorte de tapis roulant à travers lequel l'eau est aspirée, laissant les fibres constituer le papier encore très humide.
Une nappe de papier continue est ainsi constituée, selon une certaine largeur (ou "laize") et une certaine épaisseur (déterminant le grammage).
![]() |
---|
![]() |
![]() |
![]() |

PHASE DE SECHAGE
Le papier encore très mou et humide traverse ensuite des presses à rouleaux, afin de retirer mécaniquement autant d'eau que possible.
Il est alors nécessaire de compléter le séchage par des moyens calorifiques : La bande de papier circule alors sur la circonférence d'environ 50 cylindres sécheurs de grand diamètre, portés à 130 °C au moyen d'une circulation de vapeur d'eau.
Afin d'obtenir un papier moins "buvard" et plus solide, de l'amidon est déposé avant les derniers cylindres sécheurs par un équipement à rouleaux appelé «size-press».
![]() |
---|
![]() |
![]() |
![]() |
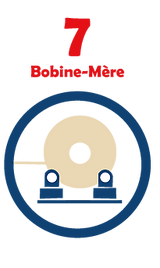
PHASE DE FINITION
La bande de papier enfin sèche est enroulée sur un mandrin métallique en bout de ligne pour constituer une bobine-mère. Les caractéristiques du papier sont mesurées et contrôlées en continu par un scanner situé juste avant cette étape.
![]() |
---|
![]() |
![]() |

PHASE DE CONDITIONNEMENT
Deuxième phase de bobinage : la bobine-mère est transférée vers la bobineuse. Le papier est déroulé et enroulé à nouveau, cette fois sur des mandrins en carton, pour constituer plusieurs bobines-filles, fermées par un adhésif et étiquetées.
Les bobines de P.P.O. (Papier Pour Ondulé) ainsi obtenues ont une laize pouvant aller jusqu'à 3,35 m environ.
La bobine-mère peut constituer 2 à 3 bobines-filles dans le sens de l'enroulement.
Dans le sens de la largeur, on peut découper plusieurs bobines-filles de "laizes" complémentaires plus petites.
Ces bobines sont alors transférées dans l'entrepôt produits finis et stockées à la verticale, avant d'être expédiées vers les clients.
![]() |
---|
![]() |
![]() |
![]() |
![]() |
RECAPITULATIF

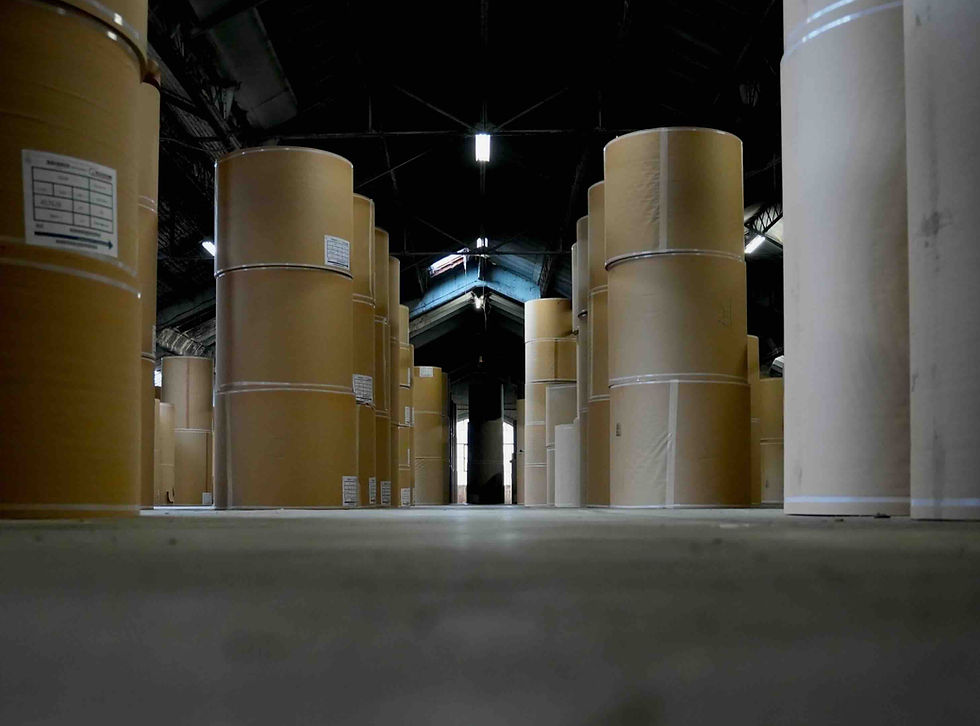